In-line washing and guaranteed efficiency
Washing tunnel allows moulds and parts washing to continuously feed the production line.
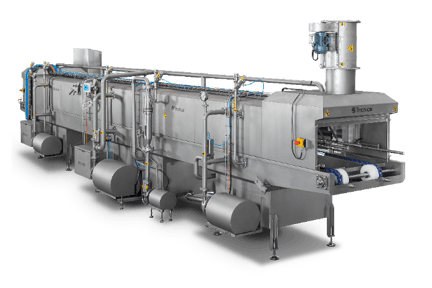
Washing tunnels adapted to the needs of the cheese factory
A washing tunnel efficiently cleans uniformly and consistently by controlling time, temperature, and mechanical and chemical action.
Moulds and parts are clean and conform to production quality standards at all times.
The tunnels are designed and manufactured in collaboration with Tecnical to meet each client's needs.
Washing tunnel stages
A washing tunnel performs a series of steps, the composition of which depends on the need for washing.
Pre-wash
At the tunnel entrance, parts are rinsed to remove whey and cheese particles. A filter recovers particles to keep the water clean.
Washing
Washing is done with a first detergent at a controlled temperature. The washing ramps equipped with spray nozzles are designed to the parts to be washed.
Rinsing
A complete rinsing of the parts with the solution returning to the pre-wash area ensures quality and saves cleaning solution.
Washing
A second detergent can be used in an Alkaline-Acid washing sequence. This step does not exist for single-phase washes.
Pre-rinse
A pre-rinse of the parts with the solution returning to the pre-wash area saves water consumption.
Sanitizing
Rinsing the parts with fresh water associated with a disinfection solution ensures their safety until use.
Advantages
Working with a washing tunnel offers several other advantages
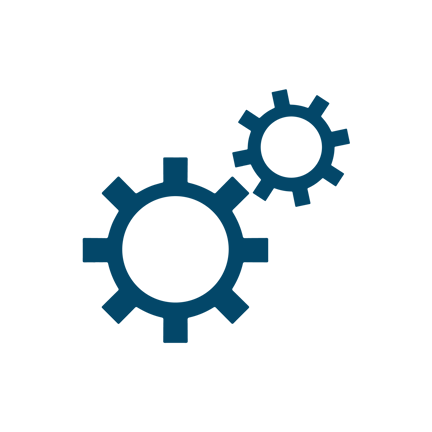
Automatic control
Detergent dosing, temperature control, conveyor speed
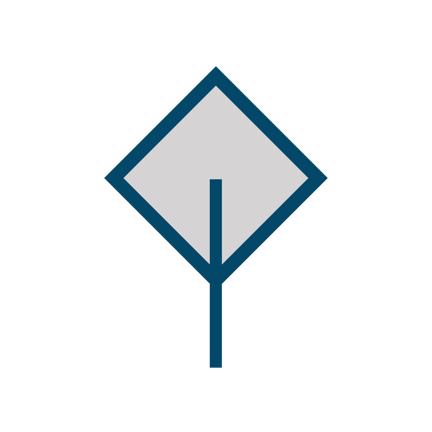
Water saving
Use less water daily while washing better

Safety
Clean parts for food safety
Your everyday challenges
When you share your goals and challenges with us, we respond by analyzing your needs and proposing high-performance, tailored solutions.